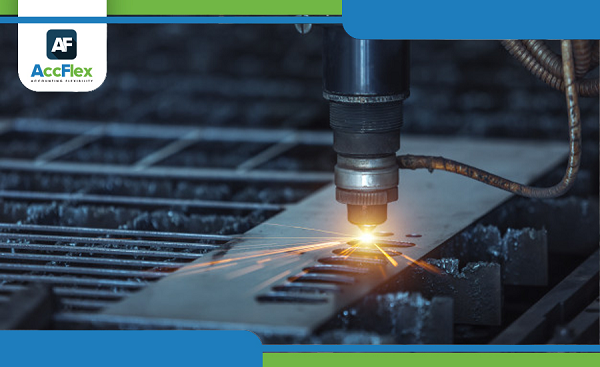
Manufacturing accounting is based on the accuracy of calculating costs, as the finished product cost is one of the most important information of manufacturing companies for pricing operations, the senior management of manufacturing companies also needs many reports necessary to making investment and financing decisions related to production operations such as decisions of expansion, renewal or production lines addition, etc., the design of AccFlex production planning software has based on a set of Help screens through which the software can be configured to add costs for each production activity, as well as Additional screens for accurate calculation, adjust and allocation of costs, in addition to a set of unique reports needed by each manufacturing activity, and the following will cover the Settings menu and Reports menu of AccFlex production planning software
First, Settings Menu
Through the Settings menu, the software is defined with the types of costs related to the company's manufacturing activity and linking them to the manufacturing process and contains three main screens, and they are
1- Product Costing screen
Through the Product Costing screen, the costs of the company's activity that the company incurs for the production of the finished product can be created, whether this cost is a direct cost related to the quantities of the finished product produced, or an indirect cost that the company incurs regardless of the quantity produced of the finished product and when selecting an indirect cost, the type of cost is determined as indirect, the software requires you to determine the indirect costs allocation base (machines working hours- raw material cost- direct labor hours or direct labor costs....) so you select the most appropriate base for allocating the indirect cost and when creating a new production process it is linked the product to its costs, whether direct or indirect and determining the value of the product allocated of each cost.
2- Indirect Costs Allocation screen
Through the Indirect Costs Allocation screen, indirect costs are allocated to production orders, once a specific period is selected and the indirect cost type is selected and a specific finished products warehouse is selected and the cost value the “Production Orders Allocation” button is clicked, all production orders that were made during the specified period are shown, and from the selected raw material warehouse, the software automatically allocates the cost to production orders, making the production costs of the finished product the most accurate.
3- Adjusting Product Costing screen
This screen is one of the most important strengths of the software, and that works to adjust any difference occurs in the material costs during the production process through withdrawing the materials from the raw material warehouse and added it to the finished product warehouse through the Adjusting Product Costing screen, the transferred warehouse and warehouse transferred to it is selected, and download all the transactions that may have a difference in cost, and through the "Adjust All Transactions" button in a split second, the software automatically adjusts the materials cost without the need to adjust the cost manually, and this screen contributes to making the manufacturing costs as accurately as possible and make it difficult to make a mistake in calculating product cost.
Second, Reports Menu
1- Cost Variance Analysis Report
Through the Cost Variance Analysis report, the difference between the standard cost and the actual costs of the finished product can be identified whether (raw materials- operating hours- direct costs and indirect costs), when creating a production process, the standard cost of producing one unit of the finished product is determined, when creating a production order, the actual costs of the production process that are incurred by the production of the product are determined, so the software automatically compares the actual costs with the standard costs, knowing the cost variances, whether material variance, cost variance, or labor variance, and analyzing these variances whether they are (positive variances- negative variances) to correct path and the cost continue as it is planned.
2- BOM Stock Report (Detailed/ Grouped)
The detailed BOM Stock report allows you to view the total quantities withdrawn from the raw materials warehouse for production orders in detail (item code- item balance- withdrawal quantities- withdrawn warehouse- raw material cost- date of withdrawal....) through this report you can track the actual cost of the production process, as well as it contributes to the redesign of the standard cost of the finished product to become closer to the actual reality, and the software shows you this report detailed and grouped to identify the quantities and the total cost.
3- Completed Work Orders Report (Detailed/ Grouped)
The detailed Completed Work Orders report gives you a detailed view of the total quantities produced through production orders added to the finished material warehouse in detail (item code- item balance- added quantities- the warehouse that added to it the finished product- date of adding the finished product to warehouse....) and through this report can follow-up the production process and identify the produced quantities and their total cost, and this report can be displayed detailed and grouped to identify the quantities and the total cost.
4- Open Work Orders Report
During the implementation of a production order, the software implements the production order in two phases, the first phase (withdrawing quantities from the raw materials warehouse) and the second phase adding quantities to the finished product warehouse, when the user withdraws the quantities from the raw materials warehouse without adding them to the finished product warehouse, the materials withdrawn from the raw materials warehouse remain in a transit warehouse called (Manufacturing process transit warehouse), which makes the production order cost inaccurate, as withdrawing raw materials that are not concerning a production process, through this report all incomplete manufacturing process that has been withdrawn from the raw materials warehouse without adding them to the finished product warehouse can be displayed and therefore back to incomplete production orders and re-clicking the "Adding Finished Product Quantities" button to complete the manufacturing process, and this report is one of the strong reports that contribute to completing the production process and then making the product cost more accurate.
5- Work Order Status Report
Through the Work Order Status report, the work order can be tracked by displaying the work order status (Closed- Work in Progress), the work order date, the executed quantity of the finished product, the quantities withdrawn from the raw material warehouse, the order number, and the work order code.
Add a comment